Wed January 12, 2022
EvoQuip
Larsen Dirtworks LLC of Foreston, Minn., knows its stuff when it comes to crushing rock.
EvoQuip customers for a few years now, it is an expert in the industry and prides itself in helping customers run smooth and lucrative operations.
The company has been running an EvoQuip Cobra 230R impact crusher, a versatile and easy to use machine that can operate in the most demanding of applications such as reinforced concrete, recycled asphalt, construction and demolition waste and natural rock.
The integrated afterscreen system on the Cobra 230R ensures the required product specification is achieved with oversize material either being recirculated back to the crusher or else stockpiled, according to the company.
Larsen Dirtworks President Mark Larsen identified some major advantages to its operations due to the use of the Cobra 230R on a range of applications.
Apron Adjustments
Larsen said that the ability to adjust apron settings depending on the application made a huge difference to them as settings for concrete and asphalt are very different. Some machines only have one adjustment.
Speed and Control
The speed at which you can adjust aprons is remarkable, Larsen said.
"It takes longer to wait for the rotor to stop than it does to adjust them, and it's so quick and easy."
He also is impressed with the ability to control the aprons by remote control from the excavator and said that this significantly increases uptime and reduces blockages.
Ease of Use
Ease of use is huge for Larsen and the ability to change screen media quickly is invaluable.
"It is super easy to change screens in the machine and they can be changed in under an hour. In jobs where no screen is required, we can remove the close circuit system in five to six minutes. We also have the ability to unload and be crushing in 45 minutes."
Larsen has found that on job sites where there is less than 10,000 tonnes it is common sense for contractors to use the Cobra 230R because of the savings that it brings on mobilization. Jobs can cost more than $10,000 in mobilization for portable setups.
"We find we can save up to 70 percent on mobilization for our contractors and it is a fast setup to begin work quickly. The Cobra 230R can be tracked between multiple piles in minimal time and the machine can be adjusted to make a variety of products depending on the contractor's needs.
"On a landfill project we had a total of 6,000 tonnes of rubble to crush; they required 2,000 tonnes to be crushed to 1 ½ in. minus and the rest to 3 in. minus. After crushing the 1 ½ in. product, we were able to remove the screen in five minutes and set the twin apron adjustments to make the 3 in. product and our excavator could not keep up with a 36 in. bucket. Tt was remarkable," Larsen said.
Larsen Dirtworks crushes for contractors and utilities companies in Minnesota, Wisconsin, North Dakota, South Dakota and Iowa and still see the major benefit in reusing the material on job sites and eliminating trucking.
On recycled asphalt product (RAP) jobs, Larsen is making 5/8 in. minus on the Cobra 230R, with production of up to 215 tph. On concrete it is making 18 in. minus infeed resulting in a product of 1 ½ in. minus with production of up to 200 tph.
Commenting on their local distributor, Ruffridge Johnson, Larsen said "Ruffridge Johnson's support has been top notch and they are always available by phone within five minutes and can usually have answers to their queries/issues within 30mins from RJ or the Terex support systems in Kentucky and Ireland.
"Mechanics are dispatched by Ruffridge Johnson, onsite within 24 hours and are very knowledgeable."
For more information, visit www.terex.com.
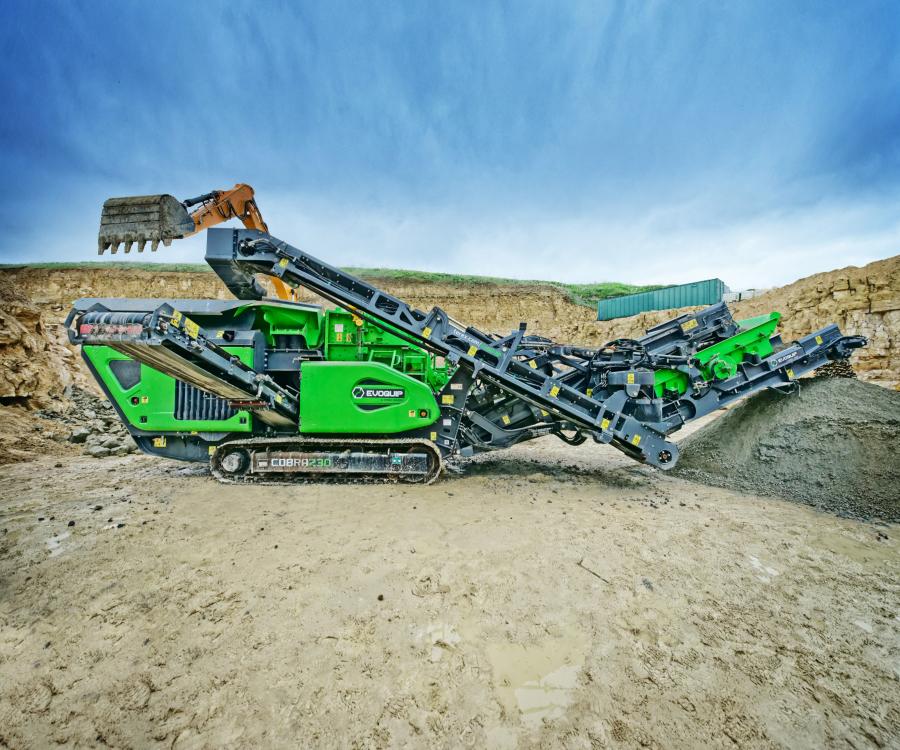
This story also appears on Aggregate Equipment Guide.